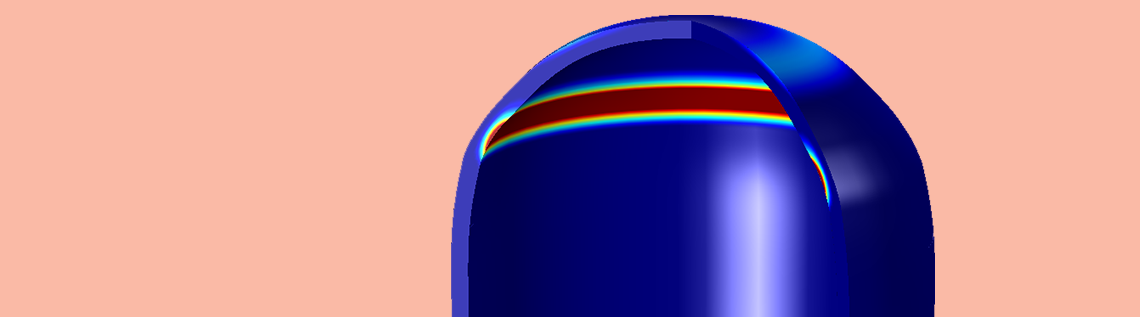
想象一下,弯曲金属纸夹,直到经过几次重复后,它完全破裂了。这是疲劳失败的一个例子,是结构崩溃的最常见类型。在更严重的情况下,这种失败会导致汽车排气管和飞机喷气发动机等结构中的崩溃或故障。为了更好地理解和预测弹性塑料材料中的疲劳失败,我们可以使用ComsolMultiphysics®软件准确地对材料和疲劳工艺进行建模。188金宝搏优惠
什么是弹性塑料材料?
弹性塑料材料结合了两种主要行为类型:弹性变形,这是可逆的变形,并且塑性变形(或可塑性),这是不可逆的,并在卸载后留下了永久性变形。为了建模这种类型的材料行为,我们需要使用一种本构之间的关系,该关系不仅将应力状态与当前的应变状态联系起来,还可以与先前积累的塑性菌株及其发育联系起来。
在受内部压力的压力容器中的塑性变形,显示弹性区域(深蓝色)和一些可塑性(红色)。
通常,当应力增加并且初始屈服应力(弹性极限)被超过时,弹性塑料的紧张远远超过弹性区域的相应应力增加。材料通过塑性变形而硬化,但是塑料状态的响应在不同材料之间变化很大。
对于金属材料,加工通常由三种不同类型的行为描述:
- 各向同性硬化,其中屈服表面随着压力的增加而扩展。张力加载也使压缩中的材料硬化
- 运动硬化,其中产量表面会翻译,但保持相同的大小。张力加载会使材料压缩较软
- 混合硬化,产量表面既膨胀和翻译
在下面的图中,我们可以可视化三种硬化类型的单轴负荷的应力 - 应变关系。在第一步中,将材料拉伸,直到达到明显的塑性应变为止。在这一点上,当前的屈服应力,\ sigma _ {\ textrm {y}},高于初始屈服应力,\ sigma _ {\ textrm {y0}}。到目前为止,应力 - 应变曲线遵循所有三种硬化类型的路径。在第二步中,载荷方向被逆转,并压缩材料,直到压缩屈服开始。
三种硬化模型的单轴负载案例中的应力 - 应变关系:各向同性,运动学和混合。
各向同性硬化,最多可以压缩材料2 \ sigma _ {\ textrm {y}}在反向屈服开始之前。随着运动硬化,最多可以压缩材料2 \ sigma _ {\ textrm {y0}}。混合硬化,压缩在两者之间,2 \ sigma _ {\ textrm {y0}} <2 \ 2 \ sigma _ {\ textrm {ym}} <2 \ 2 \ sigma _ {\ textrm {y}}}。运动学和混合硬化都会导致所谓的背应力或转移应力,这是一种新的应力水平,远离张力和压缩的屈服。在塑性发作和各向同性硬化的情况下,背应力为零。
除了这种变形硬化外,一些金属材料还表现出更复杂的行为类型。一个例子是粘塑性,其中塑性行为取决于应变率。
在ComsolMultiphysics®中建模疲劳失败188金宝搏优惠
您可以访问可用于在非线性结构材料模块中对弹性材料进行建模的材料模型的集合。但是,选择疲劳模型不仅取决于材料模型,还取决于负载特性。我们讨论了加载条件对在A中选择疲劳模型的影响以前的博客文章。
当使用非线性材料(例如弹性塑料材料)时,第一个载荷周期的材料响应通常与第二周期的材料响应不同。这是由第一个负载周期引起的,该载荷周期既可以移动产量表面并改变屈服应力。然后,连续的载荷循环可以在新的应力应变状态周围振荡或导致非弹性菌株的进一步积累。在研究疲劳时,我们必须首先找到一个稳定的负载周期,这是随后的周期的代表。因此,当对弹性塑料材料进行建模时,我们通常需要在达到稳定的负载周期之前模拟几个负载周期。
我们在另一篇博客文章中讨论了不同类型的负载周期:在非线性材料中建模热疲劳。
让我们使用COMSOL多物理学,以两种类型的硬化,运动学和各向同性硬化的类型对弹性塑料材料中的疲劳进行建模。188金宝搏优惠
用运动硬化建模材料中的疲劳
让我们看一下气缸的弹性塑料低循环疲劳教程模型。在这里,该组件的加载超出了屈服点。由于在第二个周期中已经获得了稳定的负载周期,因此材料经历了立即的稳定性。但是,稳定的负载周期包括弹性和塑性变形。这是可能的,因为该材料是用运动硬化的。这意味着屈服表面在两个位置之间移动:张力和压缩。
对于大多数涉及运动硬化的应用,必须进行完整的弹性分析。可以通过将模型分为可塑性形成的域和仅发生弹性变形的域的结构域来降低模型大小。此方法之所以有用,是因为可塑性在计算上的模型价格昂贵,因此要求我们评估另外七个自由度,而不是弹性材料中的三个位移。
通常,疲劳失败源于缺口的存在。在这种情况下,可以使用近似解决方案。例如,基于Ramberg-Osgood材料模型的塑性校正。基于弹性解决方案,这种近似方法计算凹槽处的弹性应激 - 应变状态。该方法很快,但是我们远离档位的距离越远,结果的准确性就越低。在相关的示例模型中证明了此方法:孔与一个孔的低周期疲劳分析的缺口近似。
我们可以比较下图中的两种方法。由于孔的高应变和多轴负荷条件,我们使用低周期菲古斯·史密斯 - 沃特森 - 托普尔(SWT)模型预测疲劳。两种方法的关键点的结果相似。另一方面,计算时间明显不同。对于弹性塑性模型,与Notch近似几秒钟相比,计算时间为几分钟。
基于完整的弹性分析(左)和缺口近似(右)的低周期疲劳预测。结果显示了失败的循环数的对数。两个图中使用相同的颜色量表。
与各向同性硬化的材料中的疲劳建模
在另一个教程模型中站立的接触疲劳,表面硬化的材料受到压缩载荷周期。受硬化过程的影响,经过测试的材料具有三个不同的层,具有不同的材料特性。该材料最接近表面(情况),而内部(核心)的深处很弱。在两者之间,有一个薄薄的过渡层,其中材料特性和残余应力都急剧变化。
材料的塑性特性通过深度不同。在情况层中,硬化遵循线性各向同性模型,而在核心中,它遵循指数硬化模型。在过渡层中,硬化函数是指数性的和参数化的。选择材料参数的函数,以使与情况的界面处的过渡层的材料模型对应于案例模型,并且与核心的接口对应于核心模型。
在第一个载荷周期中,材料被压缩超过屈服点,可塑性在地下水平上生长。由于屈服表面在各向同性硬化中膨胀,因此每个连续的载荷周期的幅度不如第一个循环不会引入任何进一步的可塑性,因此稳定的载荷周期是弹性的。尽管在第一个载荷周期内发展高应变,但任何连续的周期都会导致较小的应变变化。因此,可以合理地假设应力驱动的高周期疲劳模型适合疲劳评估。
在主要压缩载荷的情况下,Dang Van模型可用于疲劳建模,因为它考虑了压缩平均应力。您可以在疲劳模块中访问这些类型的模拟的Dang Van模型。
表面硬化材料中的疲劳预测。显示疲劳用法因子。疲劳的最高风险是在近表面的情况层中,深层核心层的疲劳风险较低。
通过使用Comsol多物理学模拟常见类型的弹性塑料材料的疲劳,我们可以更好地理解和预测疲劳失败的发生。188金宝搏优惠
评论(0)